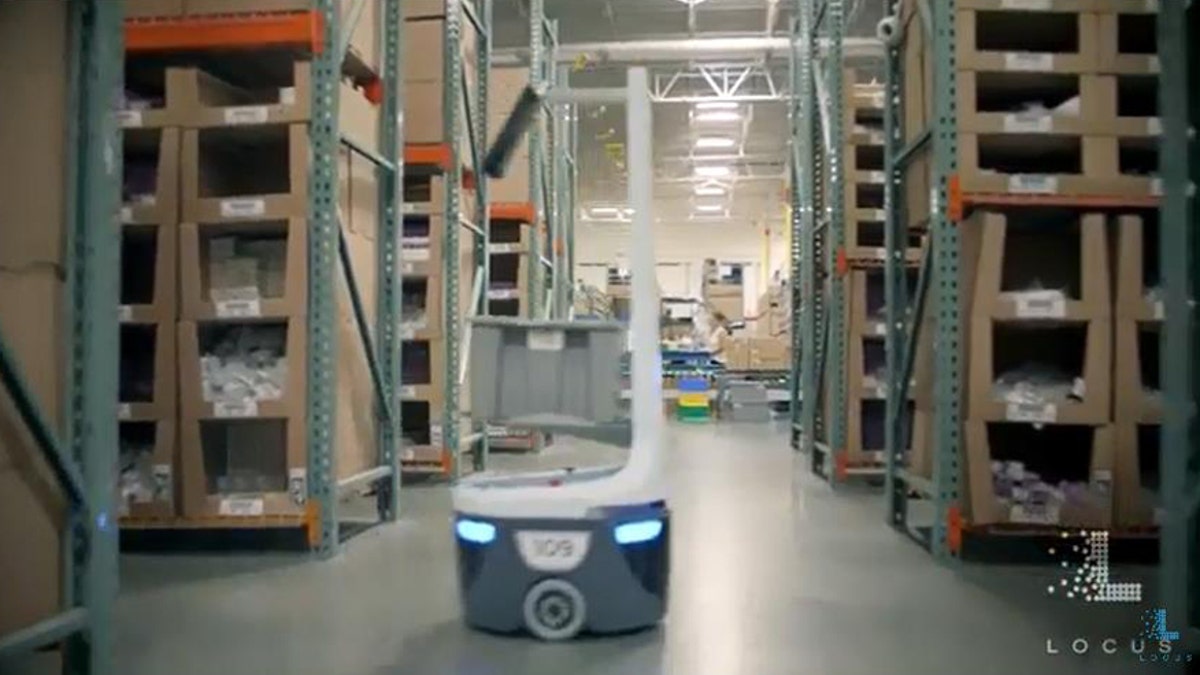
(Screenshot from Locus Robotics Autonomous Robots YouTube video)
Anyone who has ever worked as part of a team (which, in today's hyperconnected world, is virtually everyone) will know that things work better when people talk with one another. This way knowledge gets shared, collaborations become possible, and individual successes or mistakes are collectively learned from.
Why would you think that things would be any different in the world of robotics?
That's exactly what the folks at Locus Robotics have been proving with a major new software update for their factory robot LocusBots. LocusBots are autonomous warehouse robots, capable of moving autonomously through a space and then transporting items from where they're picked off shelves to the place they're packaged into boxes and shipped out. Previously this was done individually, with each robot working in isolation. Thanks to the new LRAN system -- short for Locus Robotics Advanced Navigation -- it's now a team effort.
"It's like a real-time indoor Waze for robots," Locus president Mike Johnson told Digital Trends. "With this technology, robots can literally see around the corner."
More From Digital Trends
Johnson's not referring to new X-ray abilities for the company's factory bots (although that does give us a good idea for a future startup). Instead, he's talking about a way that LocusBots can share data with one another to help make them collectively smarter. This is where the Waze comparison comes in, referring to the smartphone app which enables drivers to alert one another of road conditions as they drive.
"The challenge we're responding to is that the facilities these robots are working at are huge," Johnson continued. "We call them unstructured environments because they have a lot of equipment, a lot of people, and they change quickly. There are products coming in and products going out all the time. Our goal is to make things simple for operators. We want them to bring in robots and immediately see an increase in performance. The big change we've made to achieve this is giving robots the ability to collaborate. Rather than robots that just follow paths, these robots talk among one another, sharing information about the environment they're in, and doing this in real time."
The new system debuted at this week's industry trade show ProMat in Chicago. At the show, six LocusBots were shown navigating the floor, avoiding bumping into each other or any humans that happen to get in their way. It's an impressive demonstration of real-time route planning and crowdsourced information -- and Johnson said it works as well with 50 or 100 robots as it does with six.
It's also a nifty example of how robots can become more efficient, even without having to be physically retooled.
"While we have improved the hardware over time, this is all about the software," he said. "The great thing about software today -- including the software that we use -- is that it can be pushed out, and within minutes all of our robots have it. It's like a Tesla, where suddenly they have this new navigation system that lets them operate better."
So will robot collaboration one day go beyond this so that, for instance, multiple robots could help one another perform impromptu tasks on the warehouse floor as and when needed?
"I think that will be there," Johnson concluded. "Right now, robotics is on the early part of the adoption curve. We're seeing a lot of interest, and a lot of fascinating work done with sensors. I do think that we'll see some more interplay as these robots collaborate in new and different ways."