Fox News Flash top headlines for July 24
Fox News Flash top headlines are here. Check out what's clicking on Foxnews.com.
The inventor of the coveted N95 respirator had barely entered retirement before a global health crisis called him back to work.
With professional-grade face masks in short supply, materials scientist Peter Tsai felt obligated to return to his study — on a mission to yield the most effective methods of preserving and sterilizing the life-saving personal protective equipment he helped invent 25 years ago.
HOW THIS N95 MASK COULD PUT OTHERS AT RISK FOR ILLNESS
“If I could help, and I did not help, I would regret it for the rest of my life because people are dying,” Tsai, who patented the N95 respirator in 1995, told Yahoo Life.
Tsai, 68, from Taiwan, has lived in Tennessee for the larger part of his career, as a professor and researcher at the University of Tennessee in Knoxville.
The wearable filtration methods he developed in the early 90s were meant “for construction workers to protect them when they work in dusty environments,” he explained.
Now, the technology has become one of the most critical tools in the fight against the coronavirus — and Tsai wants everyone to know that.
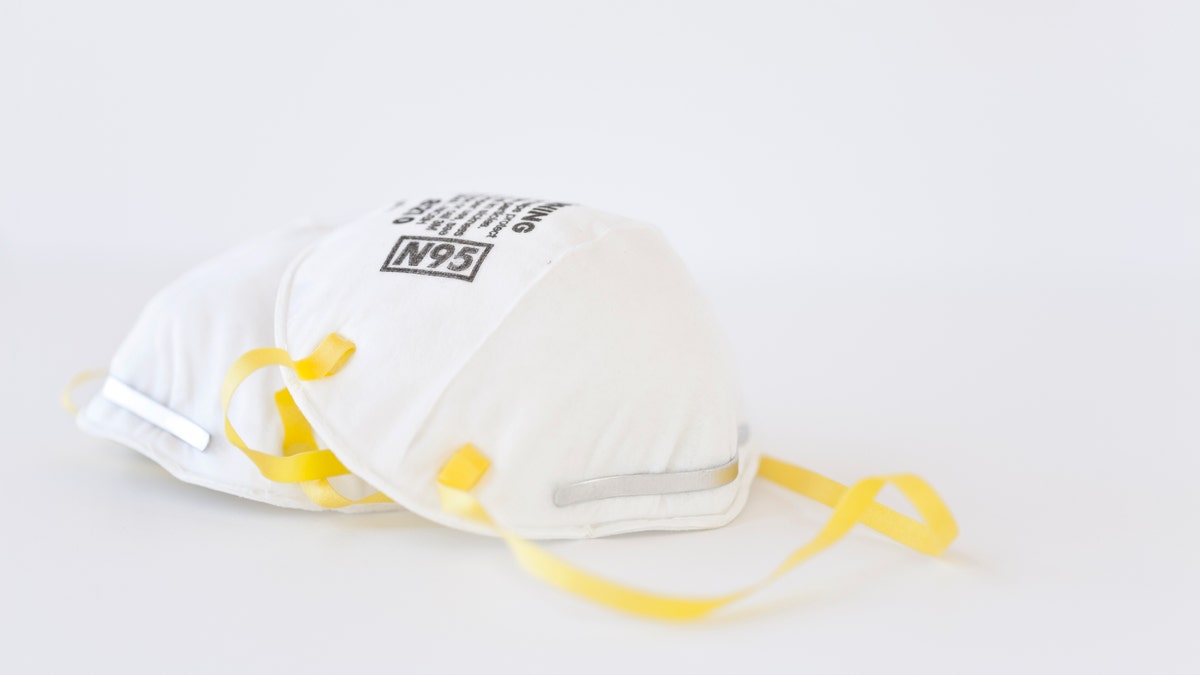
The inventor of the coveted N95 respirator had barely entered retirement before a global health crisis called him back to work. (iStock)
“Scientific data shows that if an infected person wears a mask then 95 percent of the virus is contained inside the mask. If an infected person does not wear a mask, a healthy person with a mask is only 30 percent to 40 percent protected,” he said. “Everyone needs to wear a mask.”
As the threat of the pandemic grew dire, Tsai was working “almost 20 hours a day” in his own home to find safe sterilization methods, such as boiling and baking, he told the Washington Post. His findings were recently published in the Journal of Emergency Medicine, and touted by the National Institutes of Health.
He discovered that a “dry heat method” was the most effective and durable solution to mask sterilization. N95s can be heated at 158 degrees for 60 minutes using a convection oven, essentially, and it will retain a filtering efficiency (FE) of 98.5 percent.
Another easy at-home method he found was a five-minute boil, then air-drying the mask (heat dry can warp the fit) yielded 92.4 percent FE.
Tsai was called to action, just 24 months out of retirement, by a group called N95DECON, made up of concerned scientists, engineers and health care workers who sought guidance on mask conservation. Aside from his work on effective mask reuse, he’s collaborated with the Oak Ridge National Lab, sponsored by the Energy Department, to develop a plan to scale-up their production of N95 masks. By converting their existing processing facility into one that can produce filtration cloth, the Tennessee lab can now put out 9,000 masks per hour.
CLICK HERE FOR FULL CORONAVIRUS COVERAGE
They intend to share their work so other labs can apply the technology. Recently, a fuel-filtration manufacturer — Cummins, of Columbus, Ind., — consulted with Oak Ridge to join the PPE production efforts. Now, they’re able to produce 1 million masks per day.
“If I can have this opportunity to help the community, then it will be a good memory for the rest of my life,” Tsai said. “I’m happy to do it.”