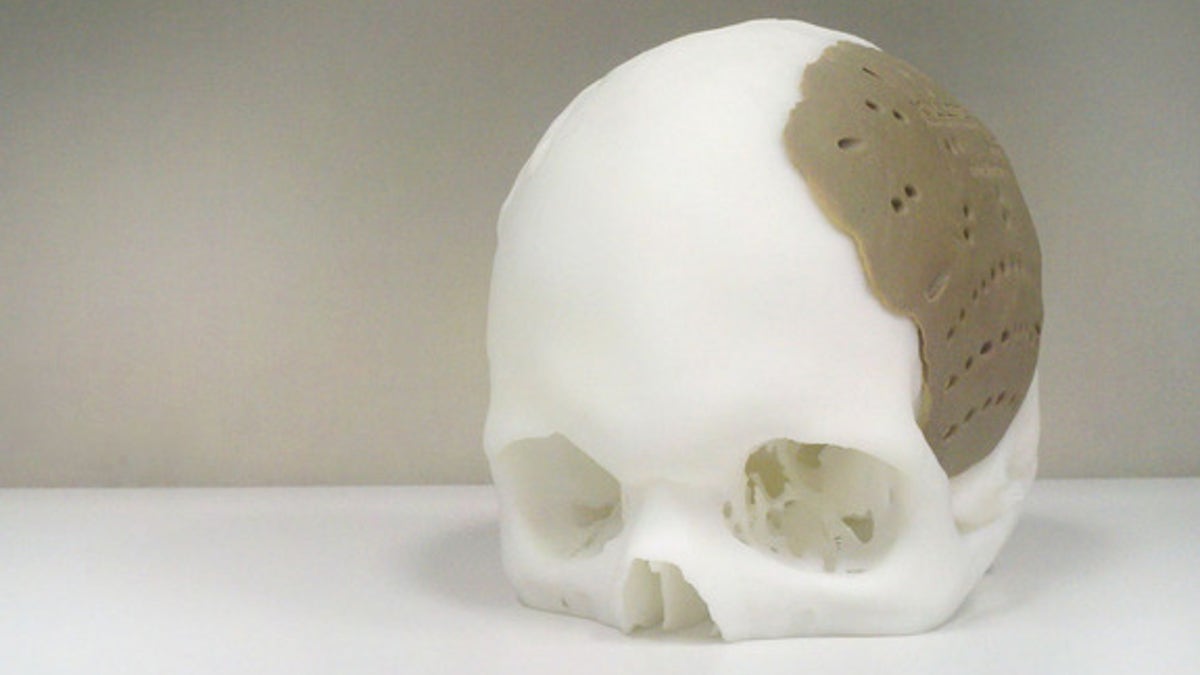
A 3D-printed skull implant. (OsteoFab)
When Kaiba Gionfriddo was just a few months old, a 3D-printed device saved his life.
Kaiba was born with a rare condition called tracheobronchomalacia, which meant his windpipe was weak, and would collapse and prevent air from flowing to his lungs. Researchers at the University of Michigan sought approval from the U.S. Food and Drug Administration for a 3D-printed tracheal splint, which they implanted around the baby's airway to help him breathe.
Thanks to 3D printing, a technology that produces objects of any shape, including medical devices highly customized for patients, from a computer model, these kinds of stories are becoming increasingly common. In order to keep up, the FDA is now looking at how it might evaluate medical devices made using 3D printers.
Another patient had 75 percent of his skull replaced with a 3D-printed implant that was customized to fit his head. The FDA has also 3D-printed devices such as spinal fusion devices and hip cups, the part of a hip impant that fits into the hip socket. [7 Cool Uses of 3D Printing in Medicine]
The FDA currently treats 3D-printed devices the same way it treats conventionally made medical devices, an FDA spokeswoman said.
"We evaluate all devices, including any that utilize 3D printing technology, for safety and effectiveness, and appropriate benefit and risk determination, regardless of the manufacturing technologies used," spokeswoman Susan Laine told LiveScience in an email. She added, "In some cases, we may require manufacturers to provide us with additional data, based on the complexity of the device."
In order for a new device to receive FDA approval, its creators must either prove the device is equivalent to one already marketed for the same use, or the device must undergo the process of attaining premarket approval. Anyone, not just medical device companies, can submit a device for approval.
But because 3D-printed products are made using a different manufacturing method than traditional medical devices use, they could require additional or different forms of testing. Two FDA laboratories are looking into ways 3D printing could affect the way medical devices are manufactured in the future.
The FDA's Functional Performance and Device Use Laboratory uses computer-modeling methods to determine how tweaks to a medical product's design could affect its safety and performance in various patient populations. Understanding the effect of these tweaks helps the FDA evaluate devices that are customized to an individual patient or group.
The FDA's Laboratory for Solid Mechanics focuses on how different printing methods affect the strength and durability of the materials used to make the devices. The lab's findings "will help us to develop standards and set parameters for scale, materials, and other critical aspects that contribute to product safety and innovation," FDA scientists wrote in a recent blog post.
3D printing makes it easier to customize devices to a patient's particular anatomy. For example, medical imaging can be used to create custom dental devices,hearingaid earplugsand surgical instruments. The FDA reviews each device as a separate submission, butmanufacturers don't have to obtain approval for each patient for whom the device has been adjusted, Laine said.
President Barack Obama launched a national effort In August 2012 among companies, universities and nonprofit organizations to support new "additive manufacturing" (3D printing) technologies, known as the National Additive Manufacturing Innovation Institute (NAMII).
Copyright 2013 LiveScience, a TechMediaNetwork company. All rights reserved. This material may not be published, broadcast, rewritten or redistributed.