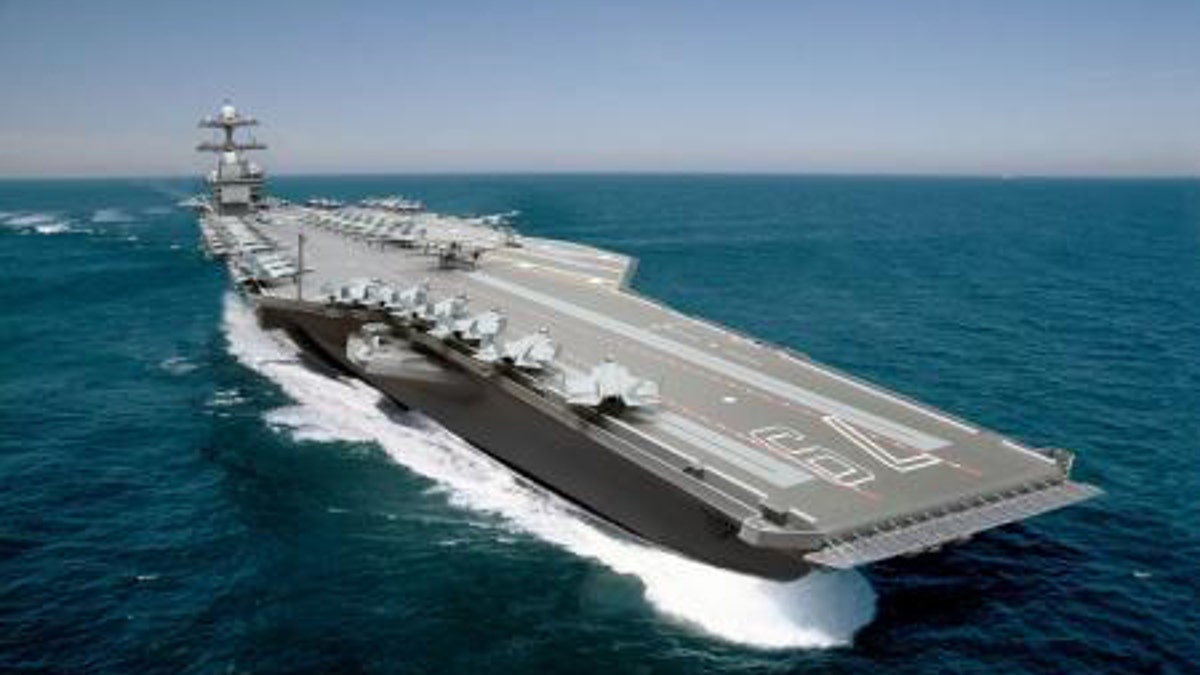
(U.S. Navy)
The Navy and Newport News Shipbuilding are working on new shipbuilding methods and making early progress with initial construction of the second, next-generation Ford-class aircraft carrier slated to enter service in March 2023 — the John F. Kennedy, or CVN 79.
The construction strategy for the Kennedy, which is thus far only 6 percent built, is using a handful of techniques intended to lower costs and call upon lessons learned from the building of the first Ford-class carrier in recent years, the USS Gerald R. Ford. The Ford was christened in November, is now undergoing additional testing and slated to enter service in 2016.
The Navy was criticized by lawmakers and government watchdog groups during the construction of the Ford for its rising costs. As of last year, construction costs for the ship were estimated at $12.8 billion, several billion dollars above previous figures.
Navy officials point out that at least $3 billion of the Ford’s costs are due to what’s described as non-recurring engineering costs for a first-in-class ship such as this. Nevertheless, they say the service is making progress with efforts to lower costs for the Kennedy.
“Through lessons learned and an intense, focused effort to improve the way carriers are built, we are confident in substantial cost reduction on CVN 79,” Rear Adm. Thomas Moore, program executive officer for carriers, told Military.com in a written statement.
Newport News Shipbuilding, which is a subsidiary of Huntington Ingalls Industries Inc., is now assembling the lower portions of the Kennedy under a construction preparation contract with the Navy.
The construction preparation contract affords the shipbuilder an opportunity to gather and purchase materials and parts for the ship while beginning initial assembly. Of the 1,128 total structural units that comprise the Kennedy, 654 of them are covered under the construction preparation contract, said Mike Shawcross, vice president of Kennedy carrier construction.
More than 230 structural units have already been completed on items such as pipe assemblies, cabling, shafts, rudders and struts, he said.
Newport News Shipbuilding is able to buy larger quantities of parts earlier in the construction process with the Kennedy because, unlike the circumstance during the building of the Ford, the Kennedy’s ship design is already completed, Shawcross explained.
In addition, one of the construction techniques for the Kennedy includes assembling compartments and parts of the ship before moving them to the dock, he said. Production lines have been started for groups of ship units that are similar, he said.
Construction begins with the bottom of the ship and works up with inner-bottoms and side shells before moving to box units, Shawcross explained. The bottom third of the ship gets built first.
As for the design, the Kennedy will be largely similar to the design of the Ford, with a few minor alterations. The aircraft elevators on the Kennedy will use electric motors instead of a hydraulic system to lower costs, Shawcross added.
Also, some of the design methods have changed such as efforts to fabricate or forge some parts of the ship instead of casting them because it makes the process less expensive, he said.